Inside Look: Mavi Jeans
•Posted on January 30 2016
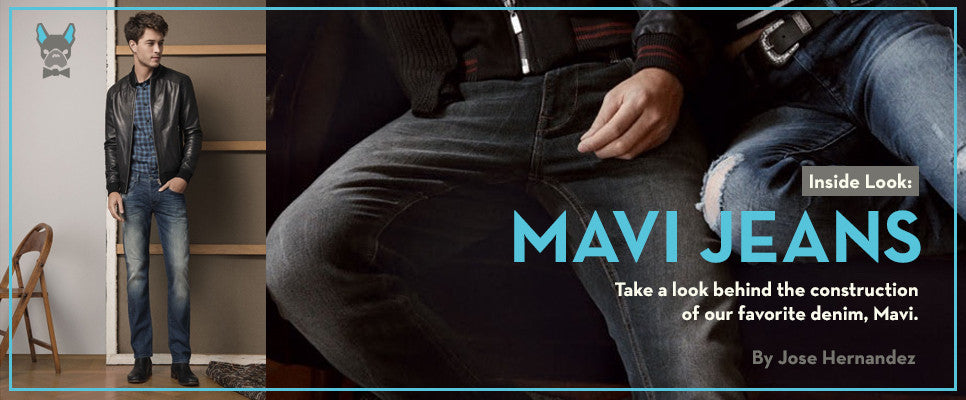
By Jose Hernandez
Denim brand Mavi Jeans was founded in Istanbul, Turkey in 1991. It’s considered a high-quality brand that combines Mediterranean details with contemporary styles that are on trend.
We were fortunate to get our hands on a tour of one of their Turkish factories to get a better perspective of how a pair of jeans goes from fabric to finished garment. Before you click on the link, let’s walk through each step of the production process:
-
Spreading: Denim comes in rolls of fabric and are laid out on giant tables to allow the fabric to relax before being cut. This is a quality measure that allows all jeans to be the same shape, once they are washed and dried. It’s recommended that this process take at least 12 hours.
-
Cutting: Once the fabric is spread and enough time is given for it to relax, it is then piled in stacks to be cut. A marker is created to be placed on top of the stack. The marker shows all of the pattern pieces that need to be cut to create a size run of denim jeans. Some companies now employ the use of laser cutters to achieve even better tolerances in their cut, providing for better quality.
-
Sewing: In the video, you’ll see the denim pieces being sewn together. Seams are sewn and pressed, zippers are added to the fly, pockets are embroidered and sewn into place with the help of machines. The very last step in the process is the addition of the waistband.
-
Quality inspection: Once the jeans are sewn together, they are checked to make sure all seams are sewn properly and there are no missing pieces.
-
Applying finishes: There are a few finishes shown in the video.
- Spraying: A red solution is sprayed on to the denim to create a fading effect. After the solution dries and is washed, the final product is a worn appearance in the sprayed areas.
- Stone washing: Pumice stones are used to create a washed over time look. Different diameters and wash durations yield different wash results.
- Sanding: Sandpaper is used to target specific areas to wear the denim. This can give a more distressed look in those areas that would typically see more wear.
-
Wash/Dry: During this step, the denim is rinsed to ensure that all chemicals and excess dye is out of the product.
-
Laser burning: This technique allows for whiskering to be etched directly on the denim. Current trends are using this technique to burn designs or patterns into the jeans.
- Final quality check: After washing and drying the finished product, the product is inspected against a “golden sample” to make sure the product is made according to the designer’s specifications. This ensures a uniform fit amongst all products of the same size.
Having this information provides a better understanding of the care and detail involved in the production of the pair of jeans we love and cherish so much. Mavi is an example of utilizing the best techniques to achieve a quality product. If you are not yet familiar with the brand, stop by our store and try them out! You won’t be disappointed.
If you’d like to learn a little more about how denim is made, check out this other very educational video:
https://www.youtube.com/watch?v=IrTh3mjeqK8
Comments
0 Comments